Locations
R360 Environmental solutions
Responsibility
Ethical Practices
All-around success is about more than just profits.
At R360, respect is the cornerstone of our business model. A respect for the environment, and a respect for the hard work that keeps the E&P industry moving. That’s why we’re committed to providing the most dependable and sustainable waste treatment options to operators throughout the nation.
By strict compliance to both federal and voluntary safety and environmental standards, we’re proud to deliver reliability that creates an all-around positive impact for our customers, employees, partners and the communities in which we operate.
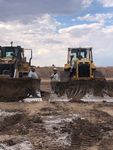
R360's Values
Safety
Improving employee performance – and overall results – through comprehensive safety standards.
At R360, we know it takes hard work to be the leading environmental waste solutions provider in the nation. And we also know that can’t be done without the dedicated employees who keep it all moving in the right direction. That’s why we’re committed to maintaining the safest possible work environments in all of our operations.
Our management team takes responsibility for the well-being of our employees through a threefold system:
- Compliance with widely held standards of workplace safety, including the Occupational Safety and Health Administration (OSHA), the National Institute of Occupational Safety and Health (NIOSH) and the Americans with Disabilities Act (ADA).
- Establishment of a system for employee feedback and a company-wide policy of periodical evaluations.
- Reinforcement of the idea that workplace safety begins on an individual level. R360 employees are responsible for their own well-being and the people around them.
Training
Orientation Training
All new hires and contractor employees begin with a safety orientation class. Written tests are administered to ensure comprehension of material and recordkeeping is maintained for future reference.
OJT/SSE Training
We have combined the On-the-Job Training process with a Short-Service Employee program to ensure newly hired employees are given opportunities to work with experienced co-workers and are evaluated through the OJT process.
Safety Compliance Training
All employees participate in regularly scheduled safety training courses, which are conducted throughout the year. We use one curriculum and only one training provider to ensure consistency in the content covered throughout our various facilities. Written tests are administered to ensure comprehension, and recordkeeping is always maintained.
Safety Meetings
We conduct formal safety meetings on a weekly basis, and tailgate safety meetings daily to reinforce company-wide policy.
Certification Training
In addition to compliance training, we train and certify all mobile equipment operators. This training is conducted by a third-party provider and consists of both classroom and practical sessions. Our courses include certification for the following equipment positions:
- Forklift operator
- Crane operator
- Dozer operator
- Excavator operator
- Backhoe operator
- Front-end Loader
- ADT (Articulating Dump Truck) operator
Stop Work Authority
All employees are empowered with full authority to stop any job they believe is being performed with compromised safety. This not only helps ensure employee well-being, but it also establishes field-wide responsibility for the safety of all operations.
Employee Involvement
All employees are empowered with full authority to stop any job they believe is being performed with compromised safety. This not only helps ensure employee well-being, but it also establishes field-wide responsibility for the safety of all operations.
Employee Recognition
In addition to safety incentive programs throughout the organization, R360 Environmental Solutions offers a variety of safety programs and incentives in every region. All R360 employees are eligible for our Annual Safety Award Program that celebrates overall safety efforts and demonstrated leadership in maintaining sound operations.
Outstanding Performance
- OSHA – Our combined OSHA Total Recordable Incident Rate (TRIR) over the last three years is below the Bureau of Labor Statistics national average.
- Workers’ Compensation Experience Modification Rates – Our combined EMR over the last three years is below the industry average.
- Lost Time Accident Records – R360 facilities throughout the country have been documented as experiencing upwards of 10 years without LTA reports.
- Customer Audits – Throughout years of service to the oil and gas industry, our companies have not only been open to customer audits, but have consistently exceeded expectations.